PHOTO
Silixa, based in the UK and the US, develops high-performance distributed fibre sensing systems for temperature and acoustic sensing in oil and gas, mining and environmental monitoring sectors. The company was established in 2007 with backing from three major investors: Lime Rock Partners, Chevron Technology Ventures and Equinor Technology Ventures.
What sets the Silixa apart from other fibre optic sensing companies, according to its Chief Product Officer, Garth Naldrett, is its primary focus on the subsurface, and the needs of the oil and gas industry.
"We were focused on the best measurement performance, so that's how we stood out," he told Zawya Projects in an interview on the sidelines of ADIPEC 2023 last month.
"Measurement performance is absolutely critical; without that, you wouldn't know whether the parameter you're trying to measure is undetectable or if your instrument isn't sensitive enough," he said.
He pointed out that Silixa's permanently installed, distributed sensing-based solutions provide reliable, continuous monitoring for oil and gas wells, and increasingly for carbon capture and storage (CCS) wells.
In the Middle East, the company has undertaken three projects thus far, one of which involves a carbon capture and storage well. Abu Dhabi-based Euro Mechanical supports the company's UAE operations. Furthermore, Silixa also collaborates with the big oilfield service companies in the region since many of its contracts are facilitated through these companies.
Naldrett said Silixa’s strategy is to build operations in places where its solutions have been commercially deployed.
"We've got a person based in the country [UAE]. As we get more and more momentum, we'll look to build that operational capability," he said.
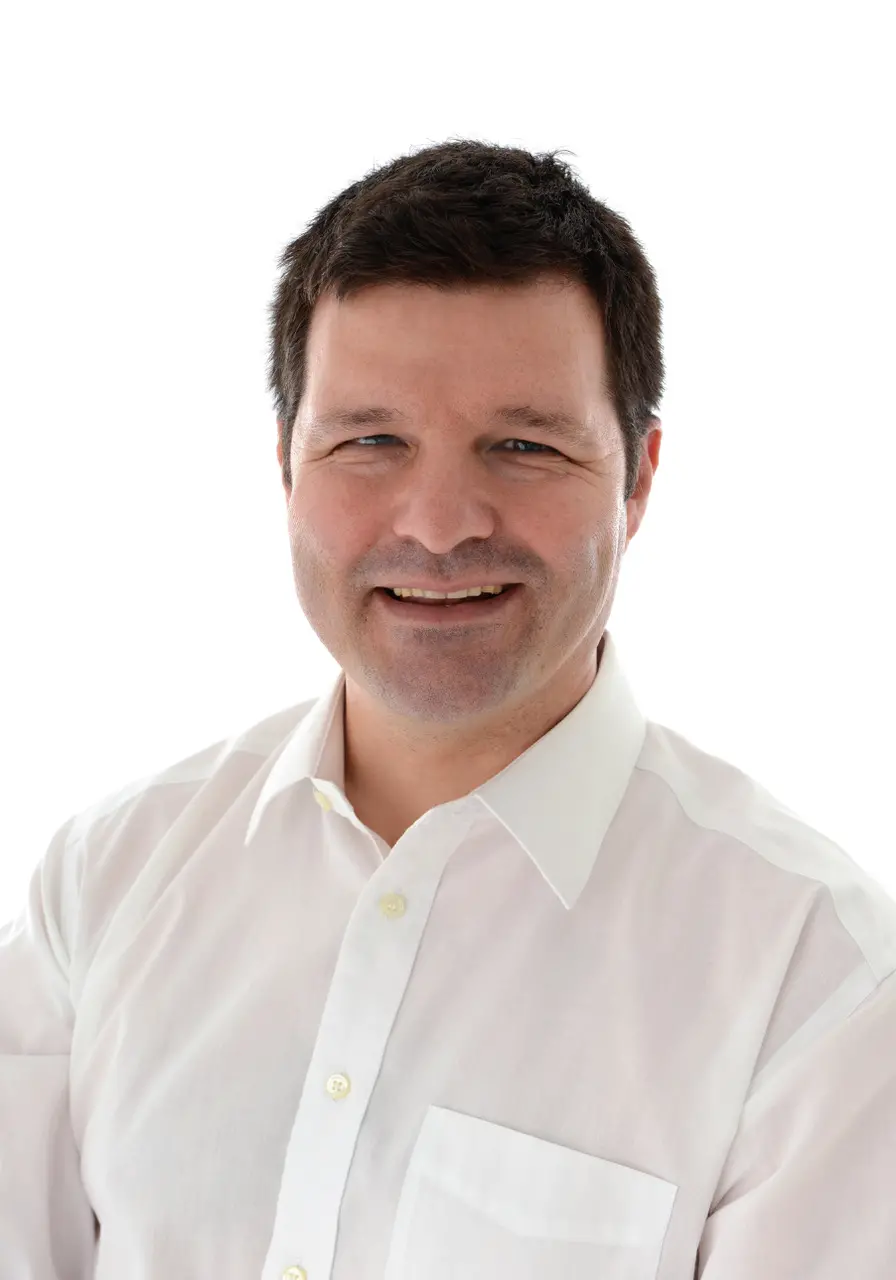
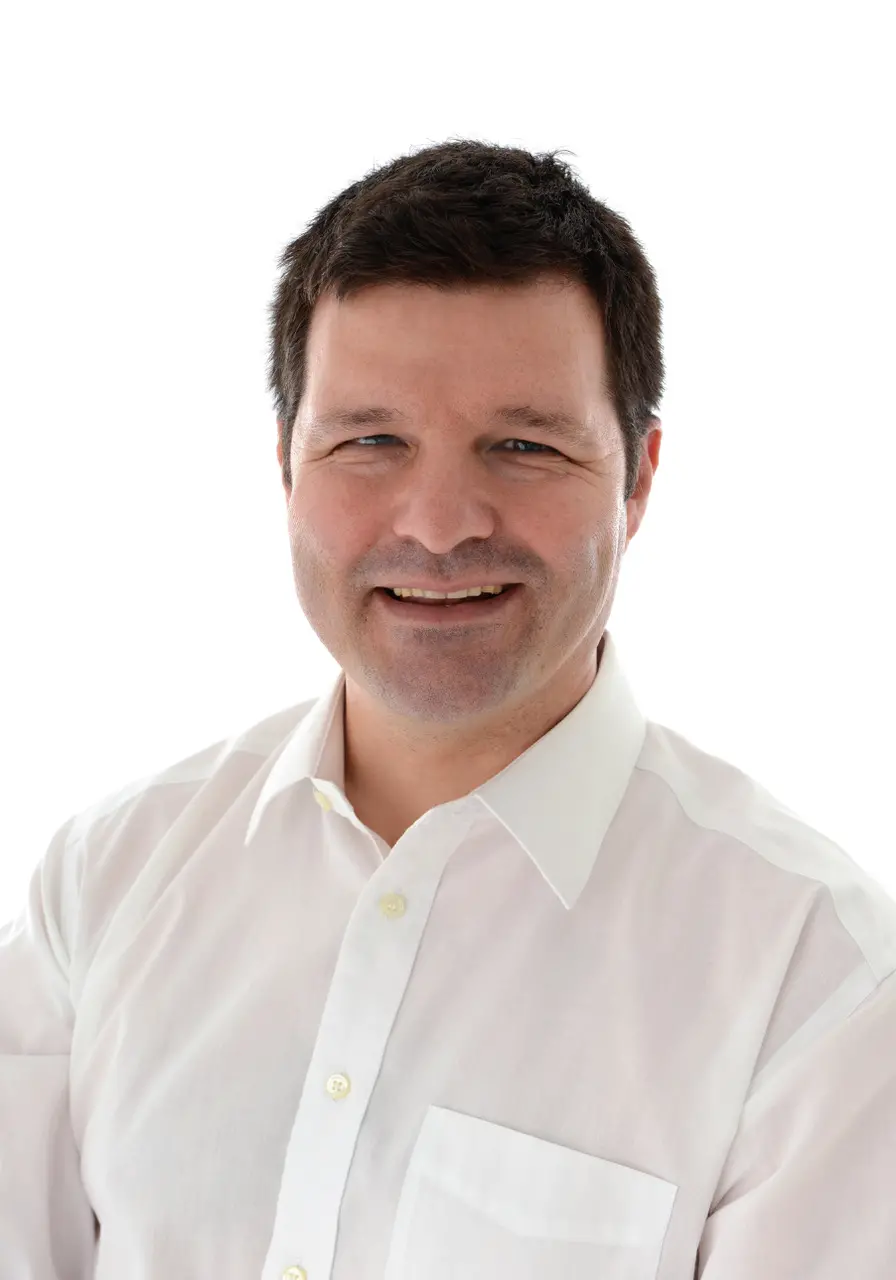
Excerpts from the interview
Could you explain the link between distributed fibre sensing systems in the energy industry and sustainability?
The link to sustainability follows a few different themes. In conventional oil and gas production, we provide data from the subsurface to optimise production. The goal is to reduce the carbon footprint per barrel by optimising the production or reducing the amount of interventions.
Conventionally, to obtain subsurface measurements, the operator would deploy a wireline truck or an on-site crew. They're episodic, there is a cost and CO2 content associated with transportation and operation of the technology.
On the other hand, our system is permanently installed and gives continuous measurements, so you get more optimisation and less CO2 to do that.
We have been involved in the CO2 sequestration sector since 2012, long before the global surge in popularity that the solution is currently experiencing. We do a lot of monitoring of the subsurface for CO2 injection, primarily to ensure that CO2 storage is done safely and securely.
When injecting CO2 into the subsurface, significant risks, such as induced seismicity, come into play. How do you ascertain that CO2 injection will not create mini-earthquakes or micro-seismic events? We monitor for leaks behind the casing, making sure that the CO2 is getting into and staying in the reservoir and not escaping to the surface, which addresses a lot of the societal concerns around CO2 injection.
Because the CO2 injection industry is relatively new, numerous uncertainties exist, particularly concerning the subsurface and the associated geoscience. It's imperative that, as an industry, we effectively address these uncertainties. Otherwise, a lot of the projects will be shut down, regulators won't approve them or allow them to continue.
An example is the Groningen field in the Netherlands, which is a conventional gas field and among the top 10 in the world. Due to a lot of induced seismicity, Groningen lost its license to operate. [According to a 2019 paper by the Hague Centre for Strategic Studies (HCSS), the gas field, which is the European Union's largest, lost its "social license to operate" due to risks caused by earthquakes induced by gas production]. We need to ensure we don't repeat that in the CO2 injection industry. That's what our technology is doing, providing the data to ensure it's safe here.
What are some of the projects that Silixa has been involved in this part of the world?
Traditionally, we didn't do much work in the Middle East. But recently, we did the first carbon capture and storage well in the region, which is actually our third project. We're very pleased with that work and hope to talk publicly about it soon. Our first was an onshore seismic flow profiling project for ADNOC using fibre optic DTS (Distributed Temperature Sensing] and DAS (Distributed Acoustic Sensing). [At ADIPEC 2023, Silixa co-presented with ADNOC on 'Using a Permanently Installed Fiber Optic System for Water Injection Monitoring on an Onshore Water Injection Well in a Carbonate Reservoir' at the technical sessions]. That was followed by an offshore project for seismic acquisition, and now we work in the region on CCS, so we are slowly building our capability.
How is Silixa pushing technological boundaries? What technological advancements are particularly noteworthy?
One part is performance capabilities. With our proprietary engineered fibre, Constellation, we achieved a 100 times improvement in signal-to-noise, which represents a massive shift in performance. The other part is the longer range, so we're trying to extend further the measurement range, which is very important for offshore subsea deployments.
Many CO2 injection projects are being piloted onshore, but as the industry scales up, I foresee these projects transitioning to offshore and subsea environments. In these settings, long-range measurements become crucial.
The third aspect is the physics of measurements. We started with distributed acoustic, followed by distributed temperature, and now, we've got distributed strain. So, we are getting more information from one cable.
How are you incorporating redundancy in your fibre sensing systems?
Redundancy holds significant importance in the context of carbon capture and storage. This is particularly crucial due to the Monitoring, Measurement, and Verification (MMV) requirements for CCS, which extend over a much longer timeframe than conventional hydrocarbon production.
In an oil-producing well, optimisation will be done in the first one, two, three years of production. After that, the production declines, and you've already done the optimisation.
The importance of the measurement in CO2 injection is likely towards the end of the field life. How do you know that the infrastructure's not getting old, that you're not starting to get leaks? Consequently, we've observed a growing demand for instrumentation with extended design lifespans, ranging from 20 to 25 years. Electronics don't have a place there, but fibre optics is ideal. It is a passive device, so there are no electronics downhole. However, that doesn't mean you don't apply diligence during selection. The same criteria applied for subsea wells in terms of a 20 to 25-year design life, cable and fibre qualification translates into CCS as well.
Outside oil and gas and CCS, are you looking at new markets?
Oil and gas and CCS are important to us in terms of critical mass. The work that we do in conventional hydrocarbon production is important because that revenue supports our CCS. Outside of oil and gas, we do a lot of environmental and infrastructure monitoring spanning areas such as mining and hydrogeology. Our revenue is evenly divided between the energy industry and non-energy markets.
We see opportunities in the trend towards electrification. Many projects are focused on reducing the carbon footprint by electrifying offshore facilities. These power cables typically incorporate fibre optics, which not only enables the transmission of substantial data volumes but also various measurements. For example, we can perform integrity measurements of those power umbilicals and optimise their power rating and capacities in real time.
Given Silixa's substantial experience and active involvement in the carbon sequestration industry dating back to 2012, could you provide some insights into the commercial progress of CCS?
In the US, we are involved in many CCS projects supported by the government through the Inflation Reduction Act (IRA). We can see that the US is getting to scale faster than some other countries, so they probably are ahead of the curve. In the UK, the announcement of £20 billion in government funding for CCS has sparked a significant increase in uptake, with 30 licenses announced in the last few months. While we have been receiving inquiries, we have yet to witness commercial deployments similar to those observed in the US.
On the other hand, only some of the projects in the US are on a commercial scale, like Occidental's, which involves direct air capture and associated CCS. But the US is transitioning from pilot projects to commercial-scale fast, and I think the UK will be the next.
Australia has also made substantial progress, and we are actively involved in some intriguing projects there. However, the CCS projects we see coming out of the Asia Pacific are slightly different.
The US and the UK capture CO2 from power generation and industrial processes, and it's the same in the UAE. But in Asia Pacific, the CCU projects tackle the associated CO2 they're producing from high CO2 content fields. For example, at Chevron's Gorgon CCS project in Australia, the world's largest, they're sequestering the naturally occurring CO2 associated with gas production to get low carbon gas.
However, irrespective of the source, the purpose of CCS remains the same – remove CO2 and store it so that it is not emitted into the atmosphere.
(Reporting by Anoop Menon; Editing by Dennis Daniel)
Subscribe to our Projects' PULSE newsletter that brings you trustworthy news, updates and insights on project activities, developments, and partnerships across sectors in the Middle East and Africa.