PHOTO
PVH's AxoneDuo Infinity solar tracking solution, launched in February 2024 at GENERA, Spain's premier energy trade show
PVH, the Spain-based global supplier of solar trackers for solar photovoltaic power projects, recently launched AxoneDuo Infinity, which the company describes "as the next evolution in tracking solutions", with its hallmarks being enhanced adaptability and flexibility.
While fixed-mount systems are initially more affordable upfront, Alvaro Casado Portuondo, PVH's Chief Revenue Officer for the Middle East, argued that solar trackers could deliver a lower levelised cost of electricity (LCOE) in the long run despite the higher initial investment.
He told Zawya Projects that solar trackers maintain the optimal inclination of the solar panels throughout the sun's translatory process to achieve a significant increase in energy production, exceeding fixed-mount systems by more than 25 per cent.
"In this regard, the initial investment in a plant with trackers is higher than a fixed structure, but the installation efficiency and the difference in energy production ensure a much faster installation payback and greater economic benefits in fewer years," he said in a post-launch interview.
He noted that AxoneDuo Infinity's string interconnectivity function offers a range of optimisation options that can be adapted to each project's budget.
"In the 1+1, 2+2, or 3+3 options, only one motor is required for every two rows, while energy production remains optimised, making these configurations the most cost-effective for reducing installation expenses," he explained.
Another critical cost advantage is that each row's mechanism is the same.
"All trackers carry the same tracker head; the motor or Cardan cable is then mounted according to the project's requirements, significantly simplifying the assembly process," said Portuondo.
He stated that since parts come pre-assembled from the factory, installation time is reduced to the minimum while ensuring maximum quality.
The PVH executive emphasised that AxoneDuo Infinity offers superior adaptability to various terrains, facilitated by fully customisable row connections, even within a single project. Based on the specific conditions of the area, rows and strings can be connected in 1+1, 2+2, or 3+3 configurations. Moreover, each row can operate independently, with the option to equip each row with its motor if necessary, facilitating the connection of up to four strings.
"Even after the project is built, the rows can be joined or separated according to identified needs or variations in the budget because each row mounts the same tracker mechanism regardless of whether they have a motor or not," he explained.
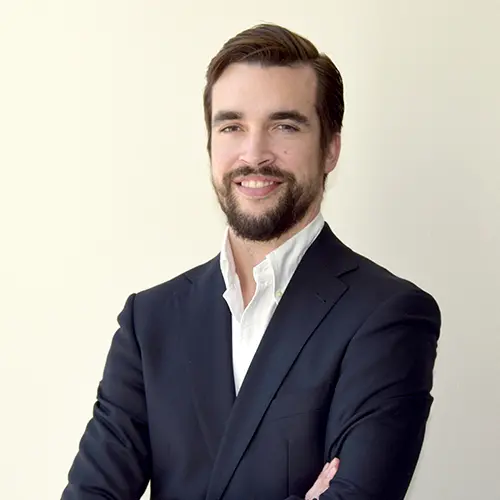
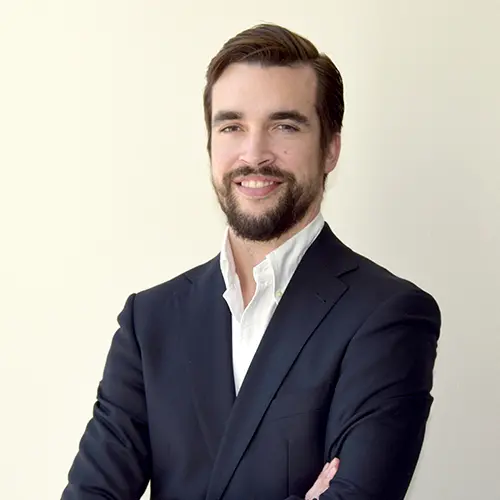
Excerpts from the interview
Can you explain how the AxoneDuo Infinity's design helps minimise costs associated with land preparation (earthworks) for a solar PV project?
We have already discussed the various row and string connection possibilities AxoneDuo Infinity offers, but another feature represents a significant innovation in PVH trackers. With AxoneDuo Infinity, we even adapt the fixed parts of the structure to accommodate the terrain undulations. This feature, called "terrain following," is based on the AxoneDuo Infinity torque tube granting up to one degree of undulation clearance to follow the terrain's contours. This is done without affecting the installation's efficiency or the tracker's strength and robustness.
How have you tackled installation costs and component integration challenges associated with solar trackers in your new product?
Our advanced in-house pre-assembly process, implemented in all our production centres, has enabled PVH to significantly reduce the number of components delivered to the site by more than 85 percent, thereby reducing solar project installation time by more than 40 percent. By assembling the most sensitive components in a controlled environment within our facilities, we provide confidence and security to our customers. It enables us to ensure maximum quality and tighter control over the operation of each tracker leaving the factory. In fact, the warranty on the designs and products of our latest projects extends up to 37 years.
On a more general note, how have you addressed the perception of solar trackers requiring more maintenance than fixed-mounts?
This is important since O&M cost has the most significant impact on LCOE. Our quality control and assurance processes are essential in this regard. PVH manufactures and assembles its trackers and control devices in its state-of-the-art factories. These are subjected to exhaustive quality control before leaving our premises.
By taking such extreme care from the beginning, we can offer our customers extensive product warranties and security that few can provide. Another critical point in maintenance is not only the detection but the prevention of incidents in the plant. Our control devices continuously monitor a series of key control parameters, and if any failure is detected in any of them, emergency protocols are activated, communicating the incident to the central control. Our devices are also equipped with AI, allowing us to anticipate and predict the critical areas where problems are most likely to arise. This way, O&M interventions can anticipate plant failures and limit production loss to a minimum.
Building on your previous answer about monitoring and control, what would 'DBox5' 's role be in a solar power plant? How does it represent a 'significant advancement' over previous models?
The DBox5 is installed on the torque tube with a straightforward installation mechanism. It is a single autonomous device that is watertight and in constant communication with the plant's operation. It receives instructions from sensors placed throughout the solar plant. These sensors are equipped with state-of-the-art algorithms that, through an artificial intelligence (AI) system, allow them to make real-time decisions to maintain maximum production at all times.
Thanks to these sensors, we can detect any incident in the plant that requires intervention. The system will immediately alert the user interface to resolve it and maintain maximum production. The PVH control system also includes a series of meteorological prediction measures to warn of extreme wind or heavy precipitation threats. Prediction is essential to activate defence mechanisms that protect the integrity of the plant and personnel.
How are challenges associated with operating in extreme weather conditions addressed?
The safety system of AxoneDuo Infinity is designed for the structure to withstand extreme wind and hail conditions and is derived from the conditions we have experienced in over 500 projects of more than 50 megawatts (MW) supplied worldwide. Depending on the climatic conditions of each area, AxoneDuo Infinity can be equipped with two different locking systems. In areas with strong winds, the panels move to a 60-degree position in the direction closest to their position. If it is an area where extreme hail occurs, the panels are positioned at 75 degrees. Both options will have a locking system that reinforces the defense position in very adverse conditions. Our experience has shown that these defense positions are the ones that best protect the structure and the installation's integrity.
Could you share some numbers regarding the increase in power production (achievable in an optimally sized solar power project based on field or laboratory-environment tests) using AxoneDuo Infinity trackers and the amortisation period? For example, what would be the cost per MW for a 1,400 megawatts (MW) solar PV plant?
Depending on the geographical location, we can expect an increase of 12-24 per cent in generation. The lower the latitude (closer to the equator), the higher the generation. The cost per MW for a 1,400 MW solar plant cannot be precisely determined without specifics as it depends on technical details like area, country, terrain, pitch, to name a few.
Lastly, what are your future plans for the region?
PVH has supplied over 5,000 MW of trackers in the Middle East region. Our products are manufactured and assembled in Jeddah, Saudi Arabia. In terms of exciting developments in store, we are planning to upgrade the capacity of the Jeddah factory to 12 gigawatts (GW) and achieve the highest local content score in the Kingdom. We are also upgrading our cutting-edge technology to adapt to future expectations.
(Reporting by Anoop Menon; Editing by Bhaskar Raj)
Subscribe to our Projects' PULSE newsletter that brings you trustworthy news, updates and insights on project activities, developments, and partnerships across sectors in the Middle East and Africa.